Integrated collection may be the future of recycling
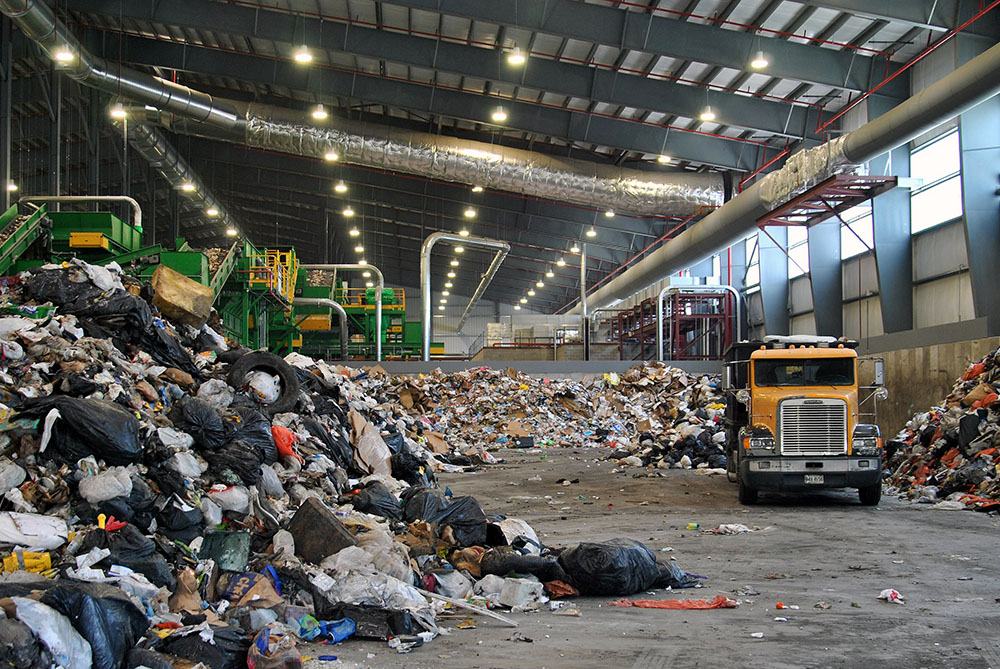
Since the 1970s, recycling has attempted to tackle the ever-increasing piles of trash in landfills by turning waste into new materials. The system has proven far from perfect over the last half-century, however, with languidly increasing rates of recovered material compared to the ballooning tons of trash produced. In order to address such challenges, the future of recycling may hinge on a new approach called integrated collection.
Coastal Resources of Maine utilizes such an integrated collection system. Their Hampden facility is the first of its kind to integrate single-stream collection with a variety of processing technologies from a company called Fiberight.
The facility accepted its first load of waste on Earth Day in 2019. Since then, they have started collecting waste from a number of municipalities, including Hampden, Brewer and Bangor. Though Coastal Resources of Maine has experienced a number of delays, the facility is projected to be fully up-and-running by October.
If Coastal Resources of Maine’s integrated collection is successful over time, it may mark a turning point for the future of recycling.
How does integrated collection recycling work?
First, residents toss trash and recyclables into the same bag and dispose according to the municipality rules. For example, Bangor residents leave their trash curbside with a limit equivalent to five, 32-gallon bags, each weighing no more than 30 pounds. Residents of neighboring Brewer, meanwhile, buy special orange tags and attach them to the bags of trash they leave at the curb for weekly collection.
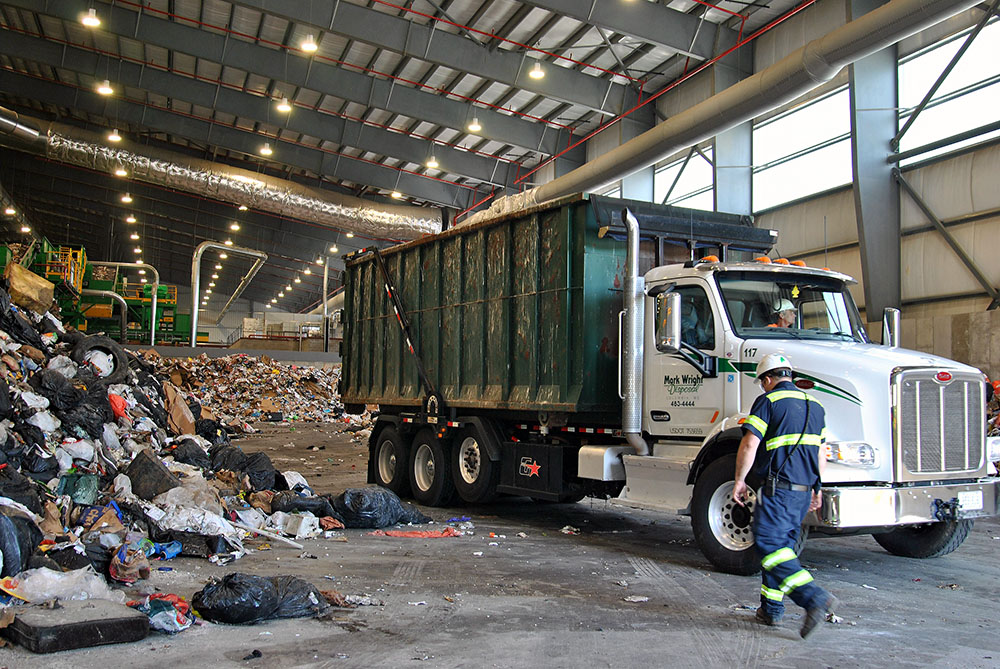
The trash is then brought to Coastal Resources of Maine’s facility in Hampden.
Next, the waste is sorted, both manually by human recycling “pickers” and using machines like magnets, compressed air vacuums and a rotating trommel with specially-sized openings to separate materials by size and weight. To control for human and machine error, the materials go through several different passes through this Materials Recovery Facility, or MRF.
Then, unusable materials are sent either to the proper processing facility or the landfill, while the usable materials are processed in one of five ways:
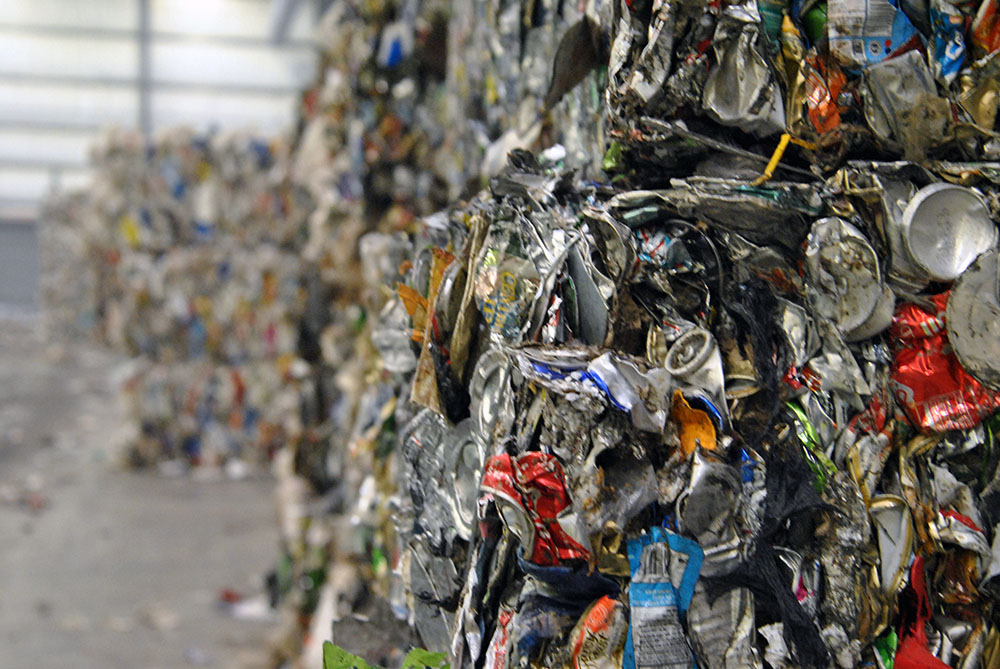
Bales:Like many recycling facilities, Coastal Resources of Maine groups profitable materials, like certain kinds of plastics, aluminum cans and, if there is a buyer, clean cardboard, and sells them as raw materials to the highest bidder.
“The bales are a marketable commodity, like any recycling facility,” said Shelby Wright, director of community resources at Fiberight’s Coastal Resources of Maine.
Glass aggregate: The rotating trommel helps filter shards of glass and other fine materials, which Wright said are ground up and used in construction projects.
In other single-stream systems, shards of glass can contaminate bales of usable materials, or they are unable to be sorted and thus relegated to landfills. The sorting technology provided by Fiberight separates glass so it has the opportunity to be repurposed.
Pulp: Paper products that cannot be baled and sold — either because they are too contaminated, like a greasy pizza box, or because the market for them no longer exists — are washed, pulped and dried on-site.
Wright explained the most facilities will not accept bales of contaminated cardboard because they do not have the tools to process the material, while the machinery at the Coastal Resources of Maine facility is able to clean contaminants off of the fibers, dry them and turn them into a versatile pulp.
The pulp can be used for a variety of applications, like post-consumer paper, kitty litter, insulation or used for biomass energy briquettes. Because the pulp is highly moldable, Wright said it is also ideally suited for the corrugated layer in cardboard.
Even when there are no interested buyers for recycled paper and cardboard, pulp can still be sold — usually at a premium, no less. Wright said that while cardboard is often sold at $20 to $30 a ton, properly dried pulp sells for about $150 to $200 a ton. This is not only because dried cellulose pulp is useful in a variety of ways, but because the technology used to dry the pulp itself is expensive and not readily available at many recycling processing facilities.
Wright noted that the Chinese recycling industry has started moving into pulp production.
“We’re one step ahead of them,” she said.
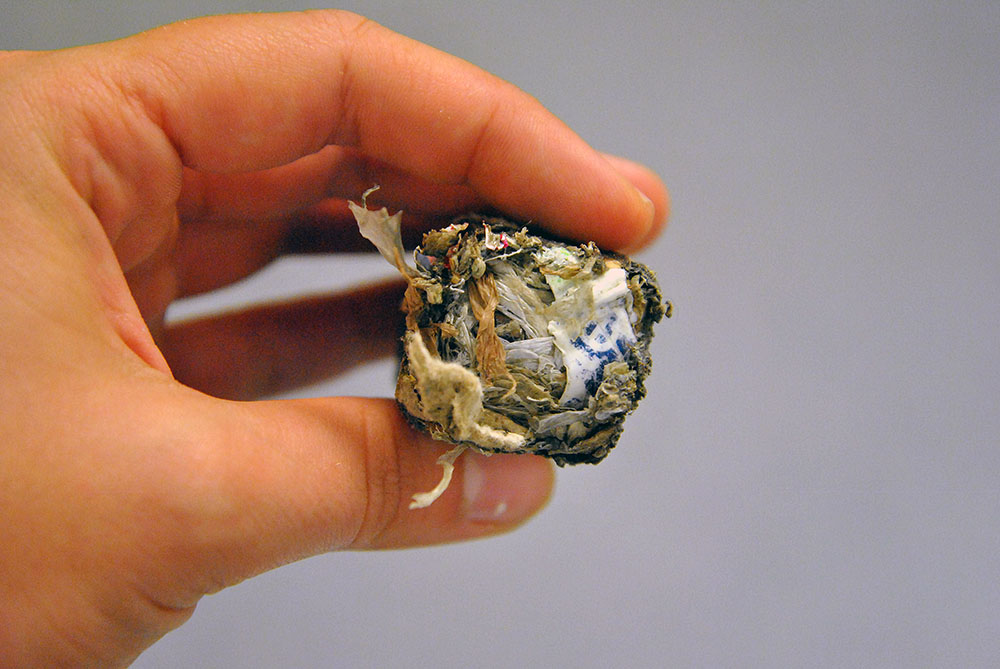
Plastic fuel briquettes: Leftover paper pulp and filmy plastic from shopping bags, sealable food storage bags and even garbage bags are formed into briquettes, which can be burned and used for energy.
While harmful materials like PVC are filtered out of the briquettes, burning plastics is still not a particularly eco-friendly practice. However, Wright argued that the briquettes substitute fuel for facilities that would have used even less environmentally friendly methods, like coal or burning tires.
“[The briquettes] melt at 450 degrees Fahrenheit, which kills any pathogens,” Wright said. “It burns hotter than coal [and] the emissions from burning tires is even higher. It is a cleaner burning plastic biofuel that takes care of plastic bags pretty efficiently.”
Anaerobic digestion: Anaerobic digestion is a process where, in the absence of oxygen, bacteria turns organic materials into energy, which will be used as supplementary fuel for internal energy production and injected into the Bangor Natural Gas pipeline.
When the pulp is rinsed and other recyclables are washed to reduce contamination, organic material is left behind in the water. The anaerobic digester converts that nutrient-rich water into energy.
Aside from creating clean energy, the anaerobic digester helps close the loop on water use in the system. The digestion process cleans the water so it can be used again to clean more pulp and other recyclables.
“Even when we have to dump water, it’s already been treated by the anaerobic digester,” Wright said.
What’s wrong with regular old recycling, anyway?
According to the U.S. Environmental Protection Agency, Americans generate more than 260 million tons of waste every year, and about 91 million tons of that waste is recycled. The recovery rate for recycled materials — the percentage of materials tossed into recycling bins that is actually processed into new products — is 35 percent.
Several factors contribute to the less-than-half recovery rate. Improperly washed food containers, for example, are often relegated to the landfill, lest the food residue gums up recycling machinery.
Well-meaning recyclers may not properly follow the recycling regulations in their area, either. Most recycling facilities sort materials by type and sell them to processing facilities to be turned into new materials. Depending on their markets, many places are limited in the types of recycled materials they can collect and successfully sell.
Wright explained that mixing recyclable materials with non-recyclable materials can “contaminate” the bales of sorted recyclable materials and make them difficult to sell.
What’s more, China, formerly the largest market for bales of recycled material, passed strict restrictions in early 2018 on the level of acceptable contamination for imported bales, a standard that many American recycling facilities consider impossible. Without a market for their materials, bales often languish in recycling facilities or wind up in landfills.
“In recycling, a bale of plastic bottles is considered contaminated if there are plastic bags in with them,” Wright said. “There are too many materials that can’t be recycled. Our system takes the guesswork out of contamination.”
Ok, how does integrated collection change that?
With the “one-bin-all-in” system, integrated collection attempts to address low rates of recycling by making recycling more convenient: no more separating recyclables from trash, and no more agonizing over whether you can actually recycle that yogurt container for so long that you wind up just throwing it away.
“As research has shown, convenience is [a] major factor in successful recycling programs,” said Travis Wagner, professor of environmental science & policy at the University of Southern Maine. “For many households, segregating, storage and transfer of an additional container is not convenient. [The integrated collection] process is designed to capture more recyclables to increase the recovery rate because it is more convenient.”
The added convenience ensures that more recyclable materials actually make it to the processing center. While other recycling facilities are limited in the materials they can process and ultimately wind up throwing recycled materials away, the range of processing technologies under one roof at Coastal Resources of Maine’s facility help get the maximum possible use out of all recyclable materials.
“We’re combining all the processing capacity into one integrated system,” Wright said.
The fact that Coastal Resources of Maine has so many processing technologies under one roof also allows for more flexibility in terms of finding markets. If one market does not work out, the materials can be used for something else. If the market for cardboard falls through, for example, Wright said the material could be broken down and sold as pulp instead.
“The market is in a state of flux, and we’re using an integrated system to cope,” Wright explained.
Hmm, integrated collection sounds too good to be true
Skeptical? Sure. At first blush, integrated collection seems a lot like single-stream recycling, where all recyclable materials are collected in a single bin (separate from the trash) without sorting. Single-stream recycling tends to raise recycling rates when compared to collection in material-specific bins. Many consider this a red herring, though, considering that single stream’s recovery rates — how much of that material is recycled into new products — are generally much lower because of the increased chance of contamination.
Integrated collection, especially at Coastal Resources of Maine, is different from single-stream, though. For starters, single-stream collection facilities were not necessarily equipped with all the sorting, cleaning and processing technologies available at Coastal Resources of Maine’s facility.
The technologies are also designed to handle many materials that are often considered unrecyclable. For example, dirty pizza boxes — a classic recycling no-no — can be broken down and dried into sellable pulp. Similarly, plastic bags are separated from other waste using several different tools and wind up being turned into plastic fuel logs.
The facility cannot process certain items, like furniture, yard waste and tires. Consumers have to drop of these materials at third-party locations that depend upon the municipality, but Wright said Coastal Resources of Maine also works to redirect the materials to the proper location if they end up at their facility, anyway.
Certain materials still wind up in the landfill, like polystyrene, more commonly known by its trademarked brand name, Styrofoam.
“I’m so glad [Maine] banned Styrofoam,” Wright groaned (Maine’s statewide recycling ban will take effect in 2021). “I hate Styrofoam.”
Wright explained that some small particulates of polystyrene may end up in the glass aggregate piles, but otherwise, it is sent to the landfill.
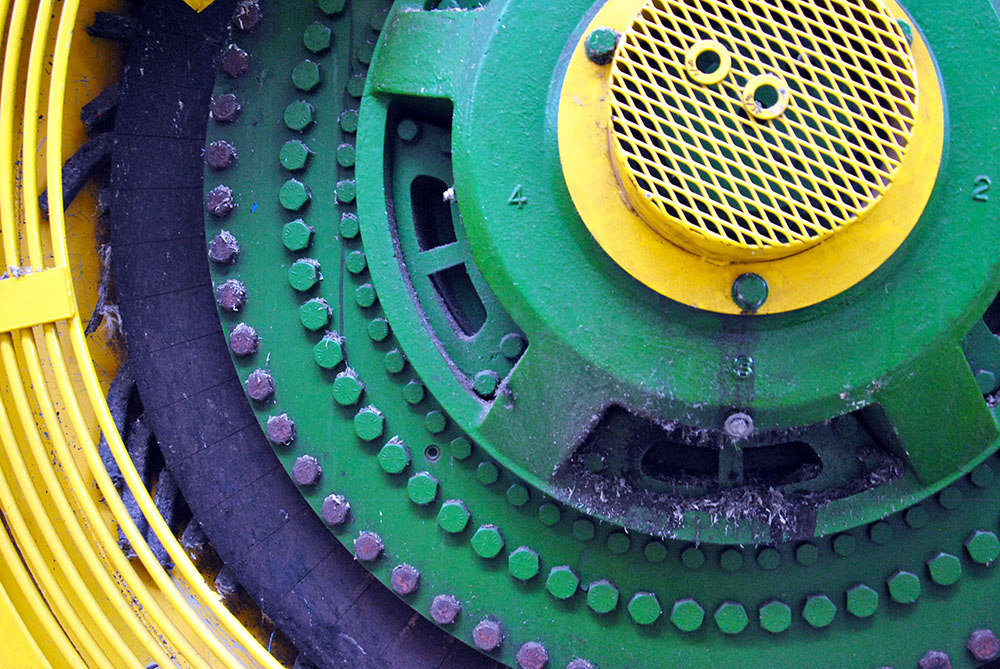
So, is this the future of recycling?
Well, we’ll see. The system is not yet processing recycled materials at full capacity, so the recovery rates are not yet known.
Wright admitted that Coastal Resources of Maine does not yet have the figures on recovery rates because the facility is not fully integrated yet, but she is optimistic.
“By law, we have to have a 50 percent diversion rate, and we have projections that are up to potentially 80 percent,” she said.
Recycling advocates and experts have lingering concerns, though. Sarah Lakeman, Sustainable Maine project director at Natural Resources Council of Maine, worries that when the plant is not operational — if the MRF requires repairs, for example — all of the material will go to the landfill because the processing stream is not diversified. She expressed skepticism as to whether Fiberight will live up to its promises of producing clean, marketable bales of recycled material, even with all the technology available.
“The recycled commodities markets are demanding clean, high-quality recycling,” Lakeman said. “Mixed waste processing [like integrated collection] tends to create a low-value, dirty, recycled commodity, making it less likely to be actually recycled.”
Lakeman asserts that integrated collection will distract consumers from reducing waste or using other — and, sometimes, more beneficial — methods of waste management, especially when it comes to organic materials.
“Separating food waste into its own bin clearly displays just how much food is being wasted, which has been proven to result in reductions in food waste,” Lakeman said. “Mixed waste processing eliminates this incentive to reduce food waste. We also miss the opportunity to recapture high-quality organic material for compost.”
Wagner also worries that the system will discourage the reduction of waste and reuse of materials. Remember: the three R’s — reduce, reuse, recycle — are a hierarchy.
“Recycling is the least preferred method of managing trash that does not involve disposal,” Wagner explained. “A concern is that making recycling so easy will result in an increase in the consumption of single-use plastics and other recyclable items.”
Whether integrated collection recycling will have these consequences in Maine remains to be seen until the Coastal Resources in Maine facility is fully up and running. Still, Wagner expressed some optimism, even in light of the potential pitfalls.
“Perhaps [Coastal Resources of Maine is] in the nascent stages of advancing technology that will show promise,” he said.